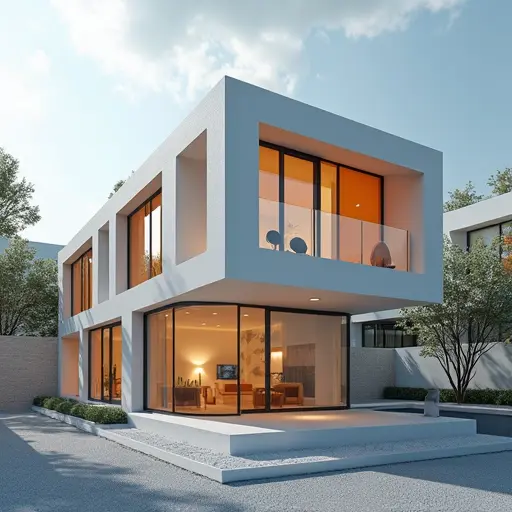
The Construction Revolution Goes Mainstream
3D printed homes are transforming from experimental projects to mainstream housing solutions. According to Grand View Research, the 3D printing construction market is exploding – projected to grow from $53.9 million in 2024 to a staggering $4.18 billion by 2030. That's a 111.3% annual growth rate!
Why It Matters Now
Housing shortages and climate concerns are driving this seismic shift. 3D printing slashes construction time by 70% and reduces labor costs by up to 80% compared to traditional methods. The UN predicts 70% of us will live in cities by 2050 – and this tech is answering the call for rapid, sustainable urban housing.
How It Works
Giant robotic arms extrude special concrete mixtures layer-by-layer, following digital blueprints. Companies like COBOD International and ICON Technology lead the charge with printers that can complete a home's structure in under 24 hours. The process uses 30% less material and generates nearly zero construction waste.
Global Hotspots
Asia Pacific dominates with 41% market share. Saudi Arabia recently built military barracks in record time, while South Africa launched a project tackling housing shortages with 15 printed homes. In the U.S., startups like Mighty Buildings secured $5 million for sustainable printed townhouses in California.
Challenges Ahead
Building codes struggle to keep pace. Material scientists are still perfecting concrete mixtures for different climates. And while printers cost $200K-$1M, prices are dropping fast as competition intensifies.
The Future Is Printed
With major players like Samsung partnering with construction firms, and innovations like ICON's new AI architect system, 3D homes are no longer sci-fi. As XtreeE plans 50 global printing hubs by 2025, your next home might just come from a printer.